Common troubleshooting for five-ply net coated whiteboard paper machine
Published Time:
2025-03-11 14:52
Source:
Troubleshooting Common Problems in Five-Ply Net Coater Board Machines
Troubleshooting Common Problems in Five-Ply Net Coater Board Machines
In modern papermaking, five-ply net coater board machines are widely used in the production of various high-quality board papers. However, during operation, these machines inevitably encounter problems that affect production efficiency and product quality. This article addresses several common problems encountered during the use of five-ply net coater board machines and provides solutions to help manufacturers improve production efficiency and product quality.
I. Uneven Coating on Paper Surface
Uneven coating on the paper surface is one of the common problems with five-ply net coater board machines. This is usually caused by improper coater head adjustment, unstable coating liquid viscosity, or uneven coater roll wear.
Solutions:
1. Check and adjust the position and pressure of the coating head to ensure that the gap between the coating head and the paper is uniform, avoiding locally excessive or insufficient coating.
2. Regularly check the viscosity of the coating liquid and adjust it according to production needs. A viscometer can be used to monitor the viscosity of the coating liquid to ensure its stability during production.
3. Regularly check the wear of the coating rolls and replace severely worn coating rolls in a timely manner. At the same time, keep the coating rolls clean to avoid impurities affecting the coating effect.
II. Insufficient Paper Strength
Insufficient paper strength will affect the performance of the board paper, especially during subsequent processing such as printing and folding, where problems such as breakage are likely to occur. This is usually caused by poor fiber bonding, improper pulp ratio, or unreasonable pressing process.
Solutions:
1. Optimize the pulp ratio, increase the proportion of long fibers, and improve the binding force between fibers. At the same time, ensure the quality of the pulp and avoid using inferior pulp.
2. Adjust the pressing process, increase the pressing pressure and time, and improve the density and strength of the paper.
3. Regularly maintain and maintain the paper machine to ensure that the pressing rolls, blankets, and other components are in good condition, avoiding insufficient paper strength due to equipment problems.
Solutions:
1. Improve the fluidity of the pulp. This can be achieved by adding an appropriate amount of additives to reduce the viscosity of the pulp and improve its fluidity. At the same time, ensure that the pulp is free of impurities to avoid clogging the mesh.
2. Adjust the tension of the wire section to ensure that the tension in each part is uniform, avoiding broken wires caused by uneven tension.
3. Optimize the temperature control of the drying section to avoid uneven paper drying and broken wires caused by excessively high or low temperatures. Advanced temperature control systems can be used to monitor and adjust the temperature of the drying section in real time.
Related Blog
Xinhailight Industry Machinery Co., Ltd. of Qinyang City - Paper Machine Technology
Qinyang Xinhai Light Industry Machinery Co., Ltd. is deeply engaged in the papermaking machinery field and understands the importance of technological innovation
Common troubleshooting for five-ply net coated whiteboard paper machine
Troubleshooting Common Problems in Five-Ply Net Coater Board Machines
Current Status and Development Direction of Domestic Paper Machine Pressing Technology
Domestic paper machine pressing technology has made significant progress after years of rapid development.
Service Tel:
Whatsapp:+86-18839165111、+86-13949691427
Company Address:Chongyi Industrial Zone, 5 kilometers south of Qinyang City, Henan Province
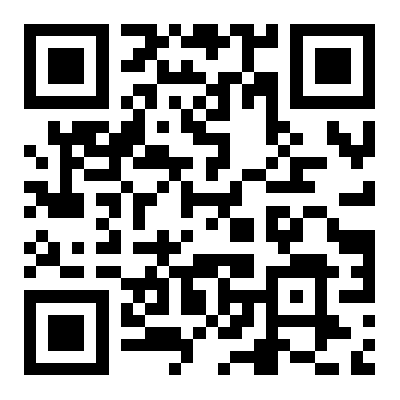
Follow Us
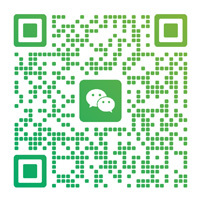